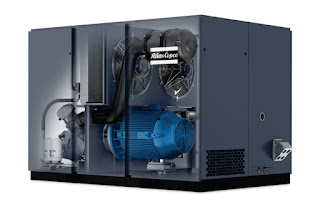
The GA 90+-160 (VSD+) oil-injected screw compressors, the latest air compressor range in Atlas Copco’s smart AIR solutions portfolio, are designed for reduced energy consumption and ease of installation and service. The range features state-of-the-art compression elements with Smart Injection technology coupled with highly efficient oil-cooled IE4 and IE5 motors that require no service interventions. The new Elektronikon® Touch controller with integrated smart algorithms further reduces energy consumption.
The latest generation of GA compressors is particularly well suited to the mining industry, metal processing and power plants where its IP66 drive train offers complete protection from environmental dust and moisture ensuring reliable operation even in the harshest environmental conditions. This reliability also provides long and trouble-free life in general industrial applications in ambient temperatures of up to 55°C.
Optimum efficiency is ensured through a highly efficient drive train, low internal pressure drops and precise control from the Elektronikon® Touch.
All components are designed for ease of service with the most commonly serviceable parts grouped together for ease of access. Furthermore, the patented portal design enables full access to all components when more extensive maintenance is required. “Subsequently, service time on these GA compressors is halved compared to similar designs leading to increased uptime and improved productivity,” notes JC Lombard, Business Line Manager – Atlas Copco Oil-free Air Division.
The GA 90+-160 (VSD+) oil-injected screw compressors are available in water- and air-cooled versions, with fixed or variable speed drive and with an optional integrated dryer.
Atlas Copco provides customers with a tip to toe 5-year Warranty Plus program on the complete machine, ensuring smooth operation in the harshest environments.
The new Optimizer 4.0 central controller replaces the company’s ES16 central controller. It enables a compressed air system to be optimised through selection of the most efficient combination of machines, such as compressors, dryers, filters, controllers, energy recovery systems, generators, air receivers, coolers and boosters. Through a highly intuitive user interface, the end-user can view the performance and energy consumption of each machine as well as of the whole system.
Optimizer 4.0 can also be monitored through a customer’s PC via LAN, a SCADA system or SMARTLINK. Moreover, it is fully Industry 4.0 compatible, enabling the Internet of Things and the digital integration of the air compressed system with other intelligent networked devices to improve equipment performance, enhance predictive maintenance and further increase energy efficiency.
Comments
Post a Comment