First battery-powered mini-excavator from Wacker Neuson wins SaMoTer Innovation Award
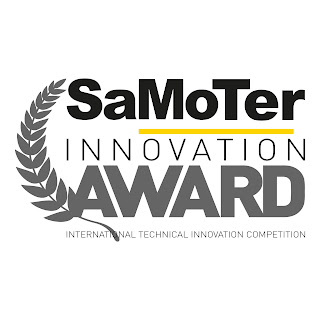
(Munich/Verona, January 2020) The first fully electric, battery-powered mini-excavator from Wacker Neuson, EZ17e, performs and handles just like a diesel-powered model. For this innovative development, the jury of the SaMoTer Innovation Award 2020 awarded the electric mini-excavator with the Innovation Award in the category hydraulic mini-excavators. Wacker Neuson is strengthening its position as an innovation leader in the zero emission segment with machines like the fully electric excavator EZ17e. In Verona, the mini-excavator was awarded with the SaMoTer Innovation Award 2020. The innovation was selected in the category hydraulic mini-excavators for efficiency and optimal integration of electric propulsion with a design identical to the diesel version and for performances identical to the classic diesel version despite ensuring null gas and noise emissions. The excavator will be the highlight product at the Wacker Neuson stand C11-C12 at SaMoTer, that is taking place from March 2